Etablierte Erntetechnik
Die Rundballenpresse ist eine etablierte Erntetechnik mit zunehmenden Stückzahlen. Die Angebotsvielfalt überfordert so manchen Neukunden bei der Kaufentscheidung. Alle renommierten Hersteller setzen auf schlagkräftige und moderne Technik.
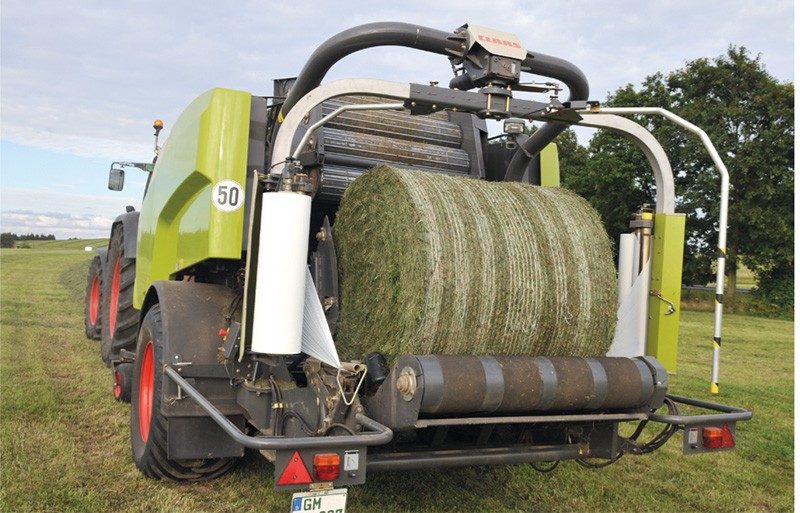
Die vielfältigen Ausstattungsmöglichkeiten können eine Entscheidung zur Qual machen. Anhängung über Zugmaul oder Kugelkopf, 540er- oder 1 000er-Zapfwelle, gesteuerte oder ungesteuerte Zinken an der Pickup, Bauform des Rotors, Anzahl Messer oder mittlere Schnittlänge, feste oder var. Kammer, Netz und/oder Folie, solo oder in Kombination pressen und wickeln, und das ist nur eine überschaubare Auflistung von Varianten und damit Fragen. Foto: Gerighausen
Die Rundballenpresse läuft in der Silage- und Heubergung der Packenpresse zunehmend den Rang ab. Gleichmäßig geformte Ballen und variable Ballendichte sind besonders bei der Heubergung gefragt. In der Silage ist sie schon lange der Favorit. Sehr hohe Dichten von über 200 kg TM/m³, gut geformte Ballen, unabhängig vom TM-Gehalt des Erntegutes, und das gute Handling in extremen Feucht- und Bergregionen zeigen die klaren Vorzüge. Daher ist der Run auf diese Technik zunehmend verständlich.
Anbau kein Problem
Anders als beim Ladewagen oder der Packenpresse, wo die zulässigen Gesamtgewichte höher sind, stellt sich die Anhängung bei der Rundballenpresse nicht als die große Herausforderung dar. Die Stützlasten sind nicht hoch und die Zug- bzw. Kraftlinie zwischen Presse und Schlepper ist so günstig, dass für die Traktion der Anhängepunkt nicht die so große Rolle spielt. Mit einem Eigengewicht von über 3,5 t ist eine Druckluftbremse obligatorisch. Einzig bei Hangabfahrten bietet der Druck der Presse auf den Kugelkopf für die Fahrstabilität Vorteile. Anders bei der PressWickel-Kombination mit ihren höheren Gewichten und Stützlasten, hier hat die Kugel klare Vorteile. Übrigens, die markanten Hersteller bieten mit einem Gestänge wahlweise den Anbau über Zugmaul und Kugel an.
Saubere und gleichmäßige Aufnahme des Futters
Wenn es um die Arbeitsbreiten der Pickup geht, waren die Rundballenpressen schon immer Vorreiter. 2 m und mehr sind hier Standard. Eine kontinuierliche Bodenanpassung über die gelenkten Tasträder ist selbstverständlich. Stärker pendelnde Varianten sind auf Dauergrünland in Überschwemmungsgebieten und in Bergsituationen für eine saubere Aufnahme ohne Verschmutzungsrisiko von Vorteil. Auch der Zinkenabstand hat in vielen Tests und Messungen keinen Einfluss auf die Aufnahme gehabt. Liegen die Erntemassen in einem kompakten Schwad von mind. 1,50 m Breite, spielt die Anzahl der Zinkenreihen eine untergeordnete Rolle.
Auch die Frage nach gesteuerten und ungesteuerten Zinken lässt sich schnell beantworten: Für Aufnahmeverluste und Verschmutzungsrisiko spielen sie keine Rolle. Für eine saubere und gleichmäßige Aufnahme hat der verstellbare Rollenniederhalter mit den Einweiserzinken die größte Bedeutung. Im Randbereich des Schwades oder bei sehr dünnen Schwaden unterbleibt das »Verrollen«. Je nach Fahrgeschwindigkeit und Windverhältnissen reduzieren sich auch die »Windverluste« erheblich.
Rotor und Schneidwerk
Auf die Durchsatzleistung, Ballenform und Dichte hat die vergleichbare Ausführung mit durchgehendem Rotor oder Zuführschnecken plus Rotor keine nachhaltige Bedeutung. Ein durchgehender Rotor ist antriebstechnisch einfacher zu integrieren. Auch die Wartung ist einfacher. Für das Schluckvermögen und den Durchsatz ist jedoch der Rotordurchmesser von großer Bedeutung. Hier sind Parallelen zum Ladewagen gegeben. Die in V-Form versetzt angeordneten stabilen Zinken entzerren das Futterschwad und unterstützen somit eine gleichmäßige Ballendichte. Wer sich heute Gedanken über die Presse von morgen macht, muss sich mit dem Schneidwerk auseinandersetzen. Das kommt nicht von ungefähr. Arbeitserleichterung und Entlastung haben auch in der Milchviehhaltung einen großen Einfluss auf die Fütterungsverfahren. Ob mit Futtermischwagen oder Futterautomaten, eine gute und schnelle Auflösung des Futters ist bedeutend für eine gleichmäßig homogene Mischung, die am Trog ein selektives Fressen ausschließt.
Das bedeutet für die Rundballenpresse ebenfalls im Minimum Ladewagenschnittqualität. Und die ist mit 35-mm-»Schnitten« definiert. Bei einer Ballenbreite von 1,20 m sind das je nach »Auslegung« 32 bis 33 Messer. Zur Auslegung: Für kantenstabile Ballen setzen einige Hersteller das erste Messer erst nach 10 bis 12 cm ein. Bei einem Schneidwerk mit 25 Messern verbleiben dann ca. 100 cm mit Messerbesatz, der dann eine rechnerische Schnittlänge von 39 bis 40 mm ergibt. Im ersten Moment nicht schlecht. Faktisch aber sind über 15 % des Futters nicht geschnitten. Diese 25 Messer auf die gesamte Breite verrechnet, ergibt eine mittlere Schnittbreite von 48 bis 50 mm. Und die spiegelt insgesamt betrachtet eine nur befriedigende Qualität wider.
Technische Details
Wer in Eigenmechanisierung seine Futterernte erledigt, kann mit bewusster Einstellung der Schwadbreite auf mehr als 1,30 m eine hohe Kantenstabilität erreichen und damit auch einen Messerbesatz bis an den Kantenbereich wählen. Bei der Bindung mit Mantelfolie erfahren der Ballen und besonders die Kanten eine zusätzliche Stabilisierung. Der Futterverlauf von der Pickup in die Presskammer geschieht über den Förderrotor. Bis auf zwei Hersteller fördern bei allen anderen die Rotoren über einen Förderboden das Futter unter dem Rotor durch das Schneidwerk, falls im Einsatz, in die Presskammer. Eine gängige Lösung mit bekannten Nachteilen.
Beim Einsatz ohne Messer sind Blindmesser für einen sauberen Messerschlitz nötig. Der Zugang zu den Messern wie auch der Messerwechsel sind sehr umständlich. Alternativ bietet der Verlauf »über Kopf« einen Messerbesatz oberhalb des Rotors an. Der Zugang und damit die Wartung und der Messerwechsel sind einfacher möglich. Die Messerschlitze setzen sich nicht mehr zu und die Messer lassen sich immer sicher einschwenken. Durch den tangentialen Verlauf muss das Futter keinen Bogen mehr passieren. Vorteilhaft für das Schluckvermögen und eine schonende Gutbehandlung, z.B. bei sehr trockenem Heu (Luzerne) und Stroh. Bei möglichen Verstopfungen hilft ein hydraulisch schwenkbarer Boden, diese Störung vom Schleppersitz aus aufzuheben. Wie auch bei den kleineren Ladewagentypen haben die Messer mit beidseitigem Schliff in der Presse den Vorteil längerer Einsätze mit scharfen Messern. Der sog. 2. Satz muss nicht mitgenommen werden.
Feste oder variable Presskammer?
Eine noch immer andauernde Diskussion. In der Vergangenheit klar geprägt durch die Hauptnutzung: feste Kammer für Silage, variable für Stroh. In den letzten Jahren haben sich die Presskonzepte jedoch angeglichen. Der Durchmesser bei den Festen bewegt sich überwiegend ab 1,30 m und mehr. Damit sind Ballenvolumen von 1,5 m³ und mehr möglich. In Kombination mit hoher Pressdichte von über 220 kg TM/m³ sind Ballengewichte Richtung 1 t und mehr keine Seltenheit. Für Silage immer noch das sicherste Presssystem. Beim Einsatz in Heu hat der relativ weiche Kern den Vorteil einer gezielt guten Nachbelüftung und -trocknung. Im sehr trockenen Stroh steigt die Gefahr des »Halmbruchs« und damit die Gefahr eines instabilen Ballens.
Anders bei der variablen Presskammer. Hier sind die Vorzüge klar im Stroh- und Heubereich. Das variable Ballenmaß und die einstellbare Dichte ergeben vielfältige Einsatz- und damit Nutzungsmöglichkeiten. Kleine Durchmesser bei Heu und Stroh für den Pferdehalter. Große Dimensionen für die schlagkräftige Einstreu von Rinder- und Geflügelställen. Ist eine Dichteeinstellung in mehreren Stufen gegeben, lässt sich auch relativ feuchte Anwelksilage noch einigermaßen pressen. Hintergrund: Die Bänder der Presse üben schon relativ früh einen hohen Pressdruck auf das Futter aus. Das feuchte Material versucht diesem Druck auszuweichen. Das Futter drängt an die Außenwand und bei langen Presszeiten pro Ballen ist dann das bekannte »Festklemmen« in der Kammer zu beobachten.
Was kann man dagegen tun?
Hier sind drei Abhilfen denkbar. Einmal über eine geringere Dichte, was der Stabilität und dem Handling nicht nützt. Dann den Ballen relativ klein machen, mit angepasster Pressdichte. Oder die beste Lösung: oberhalb der Starterwalze die Ballenbreite in der äußeren Lage immer etwas schmaler machen. Das kann mit tellergroßen Metallscheiben oder ähnlichen Lösungen erfolgen. Wer die Feuchteermittlung anstrebt, erhält dann in der Presse eine dickere abgerundete Metallscheibe, die den gleichen Zweck erfüllt. Auch die Presszeit hat Einfluss auf die Dichte und Form. Bei beiden Konzepten reicht eine reine Presszeit von 60 Sekunden zum Erreichen der höchsten eingestellten Dichte, bezogen auf einen Durchmesser von 1,30 m. Wer sein Erntegut über größere Entfernungen transportieren muss und bewusst den Rundballen gewählt hat, ist mit der variablen Presskammer gut beraten. Sie erzielt bei passender Einstellung und Technik die höchsten Dichten. Gut, eine Netzbindung zu haben. Sie hat sich bisher sehr gut bewährt. Mit ihren unterschiedlichen Konfigurationen war sie das Bindemittel der Wahl. Das ist und bleibt sie auch weiterhin für Heu und Stroh. Denn die Alternative Mantelfolie führt im Randbereich zu Schwitzwasser und damit zu Schimmel. Daher ist eine Ausstattung, die beide Varianten bedienen kann, für jede moderne Presse ein Muss.
Das aktuelle Angebot an Mantelfolie und deren Nutzung begeistert Anwender und Nutzer. Zu Recht, denn sie vereint in ihrer Wirkung nur Vorteile. Anders als beim Netz, das sich nach dem Öffnen der Presskammer um 2 bis 3 cm im Durchmesser dehnt, hält die Mantelfolie den Ballen ganz stramm zusammen. Mit vier Lagen gegenüber 2 bis 2,5 Lagen Netz hat der Ballen einen besseren Schutz bei der weiteren Behandlung. Sind beim Netz für einen sicheren Gärabschluss acht Wickellagen die Empfehlung, kann man bei der Folie locker zwei Lagen einsparen, ohne an Gasdichte einbüßen zu müssen. Im Gegenteil, beim Verladen und Stapeln sind an den empfindlichsten Stellen zehn Lagen elastisches Packmaterial, was sich nicht schnell einreißen lässt. Und bei der Fütterung und Entsorgung spielt das einheitliche Ausgangsmaterial wieder seine Vorzüge aus. Ein raffinierter Schnitt und der Ballen ist »fütterungsbereit«. Vorbei die Zeiten, wo nach der Entfernung der Folie umständlich das Netz vom Ballen entfernt werden musste. Zwar ist der Einsatz der Mantelfolie teurer als das Netz, jedoch gleicht die Einsparung der Wickelfolie den Mehraufwand fast aus.
Solo oder Kombi, was ist sinnvoll?
Diese Überschrift alleine steht für Material für einen eigenen Artikel. Denn die Beweggründe und Argumente sind sehr vielseitig und stichhaltig. Wer ressourcenschonend und nachhaltig Technik einkauft und verwertet, der muss solo pressen und wickeln. Denn ein Wickler hält bei sachgemäßer Wartung und Pflege weit über 100 000 Ballen. Ein separater Wickler benötigt einen zweiten Schlepper mit Bedienung, die in der Schlagkraft begrenzt ist und der Presse immer im wahrsten Sinne des Wortes hinterherfährt. Ökonomisch stehen dem 2 bis 3 EUR pro Ballen höhere Kosten entgegen. Das sind wiederum Vorteile für die Kombi, bei der ein Mann und ein leistungsstarker Schlepper das Ganze in einer Fahrt erledigen. Sehr zum Vorteil der Qualität. Denn hier ist das sicherste Silierverfahren vereint. Gerade aus dem Schwad aufgenommen, geschnitten, verdichtet und eingewickelt und schon kann der Gärprozess unter idealen anaeroben Bedingungen starten.
Sollte der Ballen auch noch eine Weile auf der Fläche liegen, hat der Ballen bis auf die Krähen nichts zu befürchten. Denn die guten Dichten der Ballen reduzieren bei der Aufnahme mit der Ballenklammer die Verformung und damit einen möglichen Gasaustausch. Die Untersuchungen der letzten Jahre sprechen mit klaren Ergebnissen für die Kombination. Nur das Wickeln am Lagerort mit dem anschließenden Stapeln ist qualitativ vergleichbar.
Wartung und Steuerung
Was für den Ladewagen gut ist, kann der Rundballenpresse nicht schaden. Wo Ketten sind, helfen Tropföler bei der kontinuierlichen Schmierung. Wo sich etwas dreht, ist ein Lager meistens nicht weit. Schmierpulte helfen bei der täglichen Wartung ebenso wie die teurere Zwangsschmierung.
Auch bei der Bedienung und Steuerung geht es von einfach bis komfortabel, fast vollautomatisch. Das alles hat seinen Preis. Gute Solopressen sind als Profimaschine schnell bei 70 000 EUR und mehr. Und ganz gute Kombis erreichen schnell die 100 000-EUR-Marke. Das sind Investitionen, die auch nach Auslastung verlangen. Bei einer Kombi beginnen die Auslastungen bei mind. 4 000 Ballen je Jahr, möchte man mit dem Verfahren Ladewagen konkurrieren.
Heinz-Günter Gerighausen